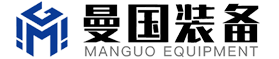
Qinhuangdao elementary chemical machinery
R&d, production, sales and service in a body's manufacturing enterprise
0086-335-7818999

Industry news
elementary chemical machinery- Your location:
- Home > News > Industry news
What challenges still lie ahead for the pre-lithiation technology, which is regarded as the inevitab
Release time:2025-01-24 10:35:00 click:
The improvement of energy density is one of the key research directions for the performance of lithium-ion batteries at present. Developing new anode and cathode materials with high specific capacity is an effective way to solve this problem. However, due to their low first Coulombic efficiency and poor cycle stability, the promotion and application of these new materials have been affected. The pre-lithiation technology of electrodes provides a cost-effective solution and has the feasibility of engineering implementation in the short term.
The Significance of "Pre-lithiation"
"Pre-lithiation" (also known as "pre-intercalation of lithium") describes the process of adding lithium into the battery before it starts working to replenish lithium ions. In a general lithium-ion battery, the storage and release of capacity are based on the reversible intercalation and deintercalation of Li+ in the electrode materials, and the Li+ required by the anode generally comes from the cathode. During the initial charging process, a certain amount of active lithium will be lost, mainly due to the formation of a solid electrolyte interface (SEI) on the anode. Therefore, the remaining lithium content will decrease during subsequent cycling. Especially, due to the formation of the SEI film, the initial Coulombic efficiency of high-capacity anodes is relatively low. In addition, due to the repeated growth/destruction of the SEI layer, significant volume changes will consume a large amount of lithium and also lead to the collapse of the active material structure.
Schematic Diagram of the Role of Anode Pre-lithiation in Lithium-ion Batteries
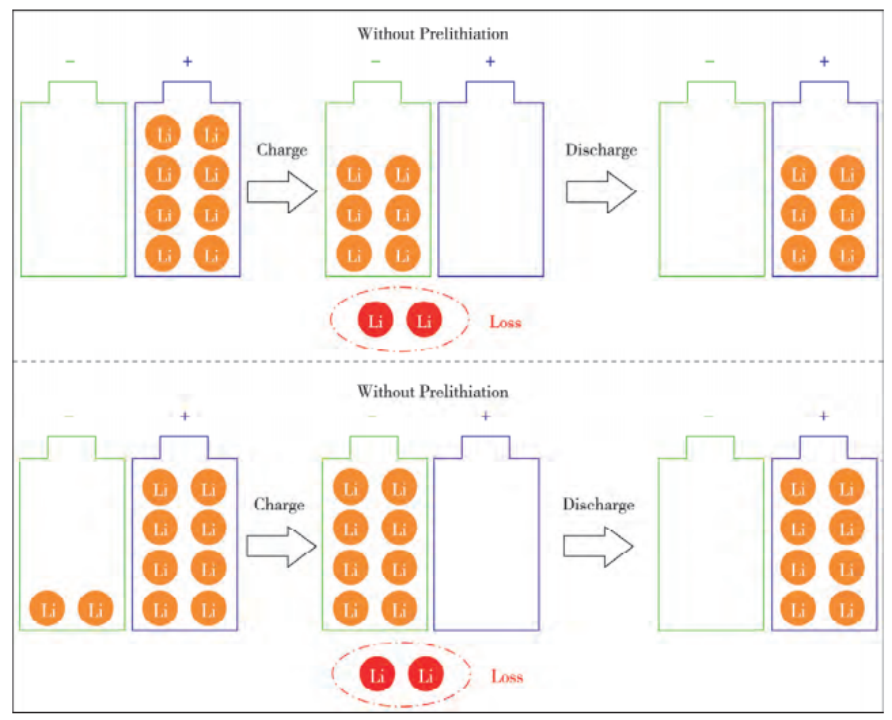
The content of active lithium lost by the anode can be compensated through pre-lithiation technology, which further ensures a higher energy density. In addition to improving efficiency and compensating for the loss of active lithium, pre-lithiation technology also has many other benefits for the improvement of the electrochemical performance of batteries:
(1) The pre-lithiated electrode reduces the internal impedance of the battery, so it has more excellent rate performance compared to the non-pre-lithiated electrode.
(2) For materials with large volume changes during cycling (such as Si), pre-lithiation can cause the electrode to expand in volume in advance, thus avoiding the collapse of the electrode structure and the detachment of the electrode material during subsequent charging and discharging cycles of the battery, which helps to significantly improve the cycle performance of the battery.
(3) Pre-lithiation treatment leads to the formation of the SEI film in advance. By artificially controlling the formation of a more stable SEI film, it helps to reduce the consumption of the electrolyte and improve the electrochemical performance.
(1) The pre-lithiated electrode reduces the internal impedance of the battery, so it has more excellent rate performance compared to the non-pre-lithiated electrode.
(2) For materials with large volume changes during cycling (such as Si), pre-lithiation can cause the electrode to expand in volume in advance, thus avoiding the collapse of the electrode structure and the detachment of the electrode material during subsequent charging and discharging cycles of the battery, which helps to significantly improve the cycle performance of the battery.
(3) Pre-lithiation treatment leads to the formation of the SEI film in advance. By artificially controlling the formation of a more stable SEI film, it helps to reduce the consumption of the electrolyte and improve the electrochemical performance.
Anode Pre-lithiation Technology
The design concept of anode pre-lithiation is mainly to pre-store a certain amount of active lithium in the anode material to compensate for the irreversible lithium loss caused by the formation of the SEI film and other side reactions, ensuring that the active lithium released from the cathode material and in the electrolyte is used for charge transfer. The common method for the anode is to directly add lithium to the anode, such as adding lithium foil or lithium powder, which are currently the key pre-lithiation processes under development. The main technical routes for anode pre-lithiation are divided into: mixing and adding lithium (adding lithium powder, lithium silicide powder, etc.), contacting and adding lithium (adding lithium foil, etc.), electrochemical lithium addition, and chemical lithium addition.
Classification and Introduction of Anode Pre-lithiation Technology
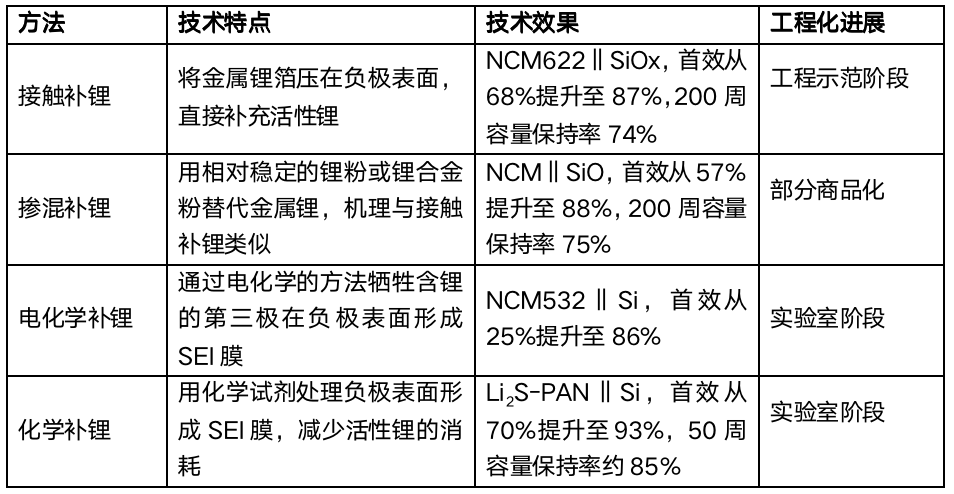
From the perspective of engineering development and commercial progress, there are currently many manufacturers directly engaged in the research on materials, equipment production, and lithium addition processes related to contacting and mixing lithium addition to the anode, and the technical maturity is relatively high. However, the most significant problem affecting the engineering progress of contacting and mixing lithium addition to the anode is the instability of metallic lithium, as well as the potential safety hazards during the production process and large-scale storage and transportation.
In addition, metallic lithium will also react with conventional electrolytes and binders, and is not compatible with existing heat treatment processes. This means that in the actual application of metallic lithium-related anode lithium addition processes, in addition to the need to carry out environmental control modifications to the production line, it is also necessary to develop new solvents, electrolytes, binders, and other materials, purchase relatively expensive special lithium addition equipment, and adjust the existing production processes. These practical engineering application problems greatly limit its transition to mass production and promotion.
In addition, metallic lithium will also react with conventional electrolytes and binders, and is not compatible with existing heat treatment processes. This means that in the actual application of metallic lithium-related anode lithium addition processes, in addition to the need to carry out environmental control modifications to the production line, it is also necessary to develop new solvents, electrolytes, binders, and other materials, purchase relatively expensive special lithium addition equipment, and adjust the existing production processes. These practical engineering application problems greatly limit its transition to mass production and promotion.
Cathode Pre-lithiation Technology
Cathode pre-lithiation refers to compensating for the irreversible loss of active lithium by adding an additional active lithium source to ensure an adequate amount of active lithium in the battery. Compared with the anode pre-lithiation technology, which has a complex process, high safety risks, and high requirements for the environment and process, the current research on cathode pre-lithiation technology mainly focuses on the development of cost-effective lithium-rich additives.
Lithium-rich additives need to meet the requirements of matching the electrochemical window, having a sufficiently high lithium addition capacity, being compatible with the existing lithium battery production environment and process, leaving little residue, and having no side reactions such as gas generation. The design concept of this type of additive for cathode pre-lithiation is similar to the solution for electrolytes to solve problems such as the electrochemical window and stability. Adding a small amount of functional additives can expand the applicable range of the electrolyte, simultaneously meeting the requirements of performance and cost. In addition, cathode pre-lithiation technology also has an electrochemical technical route similar to that of the anode.
In the actual battery manufacturing process, lithium-rich additives can be directly added during the homogenization process of the cathode slurry without the need for additional environmental modifications or process adjustments. More importantly, lithium-rich additives greatly improve the safety of the pre-lithiation process. The existing lithium-ion battery production line does not need to be adjusted at all, making it one of the most feasible technical routes for all pre-lithiation solutions in terms of engineering.
Although the current price of lithium-rich additives is relatively high, their addition amount is generally not more than 5%, but the improvement in the first efficiency, energy density, and cycle life of the battery is quite significant. With the rapid advancement of the mass production of lithium-rich additive materials, their cost is expected to be significantly reduced in the short term. While improving the energy density, it can also effectively promote the industrial application of materials with relatively low first efficiency, such as silicon-based, hard carbon, soft carbon, and tin alloy materials.
Lithium-rich additives need to meet the requirements of matching the electrochemical window, having a sufficiently high lithium addition capacity, being compatible with the existing lithium battery production environment and process, leaving little residue, and having no side reactions such as gas generation. The design concept of this type of additive for cathode pre-lithiation is similar to the solution for electrolytes to solve problems such as the electrochemical window and stability. Adding a small amount of functional additives can expand the applicable range of the electrolyte, simultaneously meeting the requirements of performance and cost. In addition, cathode pre-lithiation technology also has an electrochemical technical route similar to that of the anode.
In the actual battery manufacturing process, lithium-rich additives can be directly added during the homogenization process of the cathode slurry without the need for additional environmental modifications or process adjustments. More importantly, lithium-rich additives greatly improve the safety of the pre-lithiation process. The existing lithium-ion battery production line does not need to be adjusted at all, making it one of the most feasible technical routes for all pre-lithiation solutions in terms of engineering.
Although the current price of lithium-rich additives is relatively high, their addition amount is generally not more than 5%, but the improvement in the first efficiency, energy density, and cycle life of the battery is quite significant. With the rapid advancement of the mass production of lithium-rich additive materials, their cost is expected to be significantly reduced in the short term. While improving the energy density, it can also effectively promote the industrial application of materials with relatively low first efficiency, such as silicon-based, hard carbon, soft carbon, and tin alloy materials.
Summary
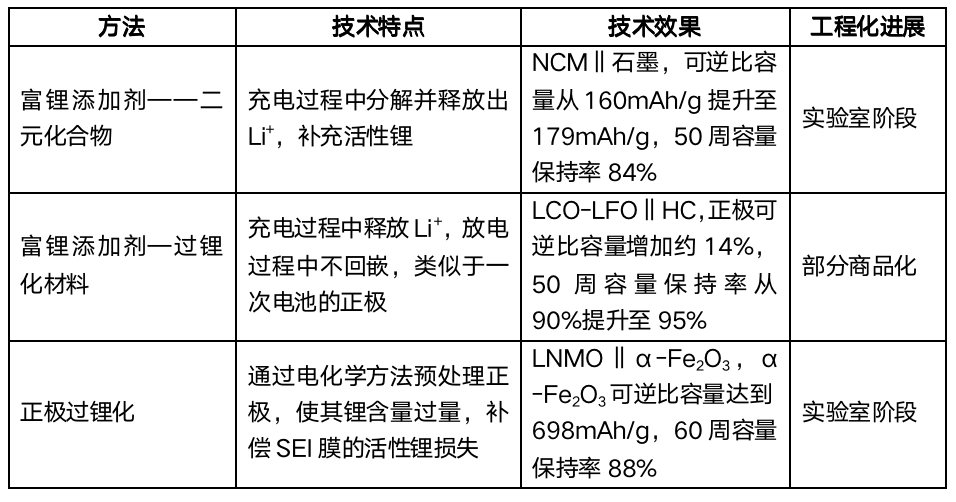
The contacting and mixing lithium addition in anode pre-lithiation has a high capacity and relatively high technical maturity. However, it requires a large cost investment, has a high difficulty in technical transformation, is complex to operate, has high requirements for the environment, and has certain safety risks. After solving the potential safety hazards in the engineering application process and overcoming the technical difficulties in materials, processes, equipment, and other aspects, it has greater development potential.
The technical advantages of lithium-rich additive technology in cathode pre-lithiation are mainly reflected in high safety and stability, as well as good compatibility with the existing battery production process. Cathode pre-lithiation technology represented by lithium-rich additives is expected to be the first to achieve large-scale application in the existing lithium-ion battery system, significantly improving the energy density and cycle performance of the existing lithium-ion battery system, and promoting the application and promotion of new electrode materials such as silicon-based materials.
The ideal choice of pre-lithiation method should ultimately depend on the manufacturing requirements, that is, it is likely necessary to find a suitable balance point between the performance gain of pre-lithiation and the additional cost. For example, if the pre-lithiation process needs to be carried out at room temperature and in air, the best choice is to use air-stable cathode additives. If the focus is on the maximum energy density and a delicate SEI film, electrochemical pre-lithiation may be the best choice.
Regarding safety and aging behavior, it is very important to control the degree of pre-lithiation, because an excessively high degree of lithiation may lead to the formation of high-surface-area lithium deposition, which will cause safety problems in the battery and a low cycle life of lithium metal batteries. In addition, when exploring the application of pre-lithiation in the process of large-scale battery manufacturing, other aspects also need to be considered: 1) Inactive residues may increase additional mass and volume, which will reduce the energy density; 2) The high reactivity, toxicity, and danger of some of the chemicals and methods used require special preparations and safety measures; 3) The use of dry air or an inert atmosphere during the processing will undoubtedly lead to an increase in cost.
The technical advantages of lithium-rich additive technology in cathode pre-lithiation are mainly reflected in high safety and stability, as well as good compatibility with the existing battery production process. Cathode pre-lithiation technology represented by lithium-rich additives is expected to be the first to achieve large-scale application in the existing lithium-ion battery system, significantly improving the energy density and cycle performance of the existing lithium-ion battery system, and promoting the application and promotion of new electrode materials such as silicon-based materials.
The ideal choice of pre-lithiation method should ultimately depend on the manufacturing requirements, that is, it is likely necessary to find a suitable balance point between the performance gain of pre-lithiation and the additional cost. For example, if the pre-lithiation process needs to be carried out at room temperature and in air, the best choice is to use air-stable cathode additives. If the focus is on the maximum energy density and a delicate SEI film, electrochemical pre-lithiation may be the best choice.
Regarding safety and aging behavior, it is very important to control the degree of pre-lithiation, because an excessively high degree of lithiation may lead to the formation of high-surface-area lithium deposition, which will cause safety problems in the battery and a low cycle life of lithium metal batteries. In addition, when exploring the application of pre-lithiation in the process of large-scale battery manufacturing, other aspects also need to be considered: 1) Inactive residues may increase additional mass and volume, which will reduce the energy density; 2) The high reactivity, toxicity, and danger of some of the chemicals and methods used require special preparations and safety measures; 3) The use of dry air or an inert atmosphere during the processing will undoubtedly lead to an increase in cost.